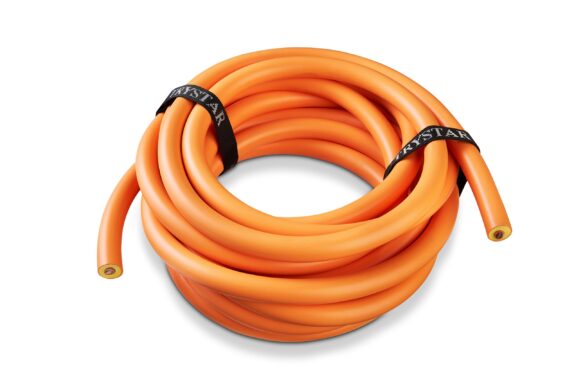
Cables
Designed to withstand the rigors of industrial and rental applications, our cables feature an inner insulation layer in a contrasting color designed to alert you to cuts, nicks and excessive wear on the outer insulation jacket, offering exceptional durability and flexibility.